Tools and Test Equipment recommended for ex repair work.
When working on an Ex d apparatus, the following measuring equipment suitable for the size of machine being inspected:
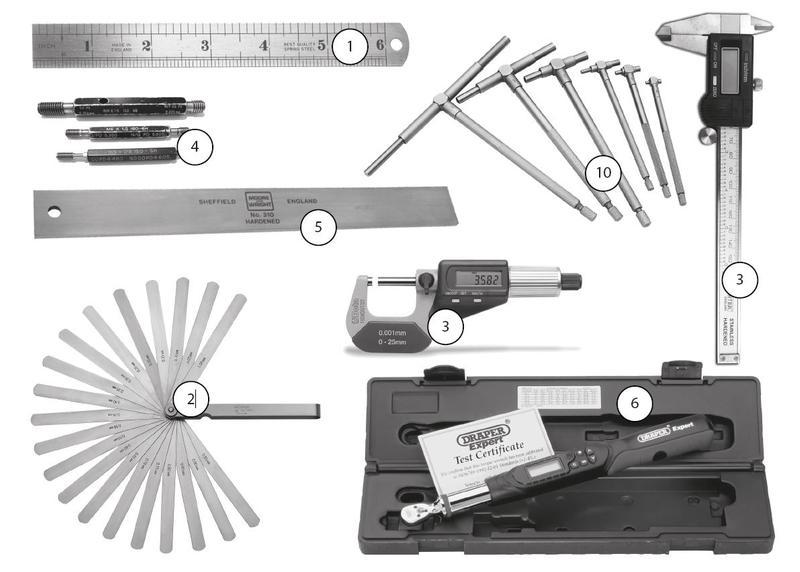
Accurate measuring equipment with an in date certificate of calibration must be used for ex repair work.
- Engineer’s Rule: inch and metric
- Feeler Gauges: inch and metric.
- Calibrated Digital or Analogue Vernier Callipers/Micrometres: Strongly recommended for measuring metal thickness, outside and inside diameters. Appropriate to the frame sizes being repaired. Micrometres both internal and external can be used and are more accurate for measuring small flamepath dimensions.
- Calibrated Screw Thread Gauges: Go and no-go, as appropriate.
- Calibrated Engineering straight edge: Used to inspect that surfaces are flat.
- Calibrated Torque wrench Kit.
The following Test Equipment will also be necessary:
The test panel should have the ability to carry out no-load and locked rotor tests on motors, using a Variac and a suitable supply for the full load current that may be required. There should be a method of securing the motor, and locking the rotor.
Optional equipment includes:
-
Magnetic particle crack testing equipment or dye testing equipment: Required if welding or metal recovery methods are used.
-
Engineering surface plate or table: Suitable for handling end shields, and motor foot mountings etc.
-
Depth Gauge if the Vernier’s used do not have such a facility.
-
Telescopic Gauges ideal for the measurement of internal diameters.
-
Manual Calliper and divider set.
-
Over Pressure test rig.
-
Coordinate Measuring Machine (CMM)
The above items should cover the range of equipment repaired and assumes the operator has the experience and skills to use correctly and accurately.
If accurate measurements are needed e.g. the flamepath is close to being unacceptable, then using a micrometre is more accurate than Vernier’s.
If major reclamation or modifications to an enclosure are being made it may be a requirement to perform a pressure test. Guidance on the equipment needed and the procedure to adopt is covered in the IEC BS EN 60079-19 standard and IECEx service facilities guidance documents. Section 5.2.1.2 of BS EN or IEC 60079-19.
Post Ex repair checklist
To give an idea of all checks to be completed before an Ex repair can be signed off, please refer to the table below:
Inspection/Test |
Completed as Part of a Repair/Overhaul |
Required as Part of Re-commissioning / In-Service Maintenance Programme |
Winding Continuity Test |
Yes |
No |
Insulation Resistance Test |
Yes |
Yes |
Insulation Class Voltage Withstand Test/Impulse Test |
Yes |
No |
No Load Test |
Yes |
No |
Locked Rotor Test |
Yes |
No |
Vibration Test |
Yes |
No |
Bearing Running Temperature |
No |
Yes |
Bearing Noise |
Yes |
Yes |
‘k’ Value Measured |
Yes |
No |
Internal Flamepaths |
Yes |
No |
Gaskets |
Yes |
No |
Radial Air Gap |
Yes |
No |
Fan Clearance |
Yes |
No |
Rotor Balance |
Yes |
No |
Lubrication |
Yes |
No |
IP |
Yes |
Yes |
Cable Conduit |
Yes |
Yes |
Lift Eye Bolt |
Yes |
No |
Endshield Bolts/threads |
Yes |
No |
Terminal Box Connections |
Yes |
Yes |
Terminal Clearances |
Yes |
No |
Terminal Box Insulations |
Yes |
No |
Approved Modifications |
Yes |
No |
Reclamation Drawings |
Yes |
No |
Repair Records |
Yes |
No |
Overload Trip Setting |
No |
Yes |
Control Gear Compliance |
No |
Yes |
Alignment |
No |
Yes |
Stable On Load Running Temperature |
No |
Yes |
On Load Noise Level |
No |
Yes |