Sulzer delivers the ‘Wow-Factor’ with 2MW Falkirk test facility.
The bridge of the 2MW test bed is functional and delivers the ‘Wow-Factor’.
Like a stack of cards growing higher and higher – the Sulzer Falkirk test bed was becoming increasingly unstable. Hemmed in by legacy brick walls and 25 years of modifications and add-ons, meant it was time to bite the bullet and rebuild the service centre’s testing capabilities from the ground up.
On January 25th the workshop doors were flung open to welcome selected guests and customers to view the shiny new test bed. It was clear that it had been designed with ‘wow factor’ in mind. The days when workshops were built for purely utilitarian purposes are clearly over, as visitors look to be impressed with the cutting-edge facilities.
Besides the fresh white paint opening up the workshop space after decades of gloomy dark walls, the glass walled test centre housing an über stylish control centre and customer reception cannot fail to impress. The sleek LED-lit control centre wouldn’t look out of place in the Starship Enterprise, whose bridge looks out onto a generously sized 2MW test bed.
NOTE: Meet those responsible for the test bed installation at the AEMT Scotland meeting on Wendesday, 16th May. Click the banner below for more information.
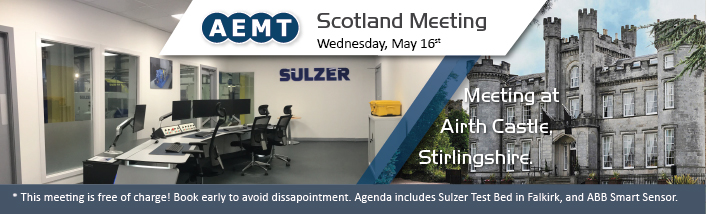
Keeping in control
It would be prudent to wonder whether there is a need for such an extravagance. After all, can a motor load test not be done onsite, where the machine can be put against real running conditions?
Static tests can be run to check winding resistance, insulation resistance and surge comparison test to test the stator of the machine.
When checking a machine under full load, a much more comprehensive picture of the motors required performance can be built up. The test is particularly relevant to check critical machines that are going to be difficult to return to the workshop after fitment either due to location, confined space, lifting gear requirements, shipping, offshore etc. Tests can include efficiency, noise and temperature rise measurements, indirect load tests, excess current, torque tests, and torque/speed tests.
Sulzer has invested in a controlled environment. On site testing where the environment cannot be controlled, will throw up a lot of uncertainties in the readings, leading to unreliable results. Getting a machine up to normal running temperature can take 4 to 6 hours, and to keep a machine on full load on site could be difficult.
In a controlled environment, the ambient temperature is known, while the load can be accurately applied. There is also the benefit of being able to test the equipment for a full working day or over an extended period.
More importantly – the test bed’s stiffness is known and factored against the machines vibration and noise levels, whereas on site vibrations would cloud the results. Another aspect to consider is being able to measure the temperature of the windings within 2 minutes of stopping, which is much, much, easier to do in a controlled environment, resistance temperature detectors don’t always give the complete story.
As part of the upgrade project, the test area was equipped with the latest monitoring controls and safety equipment, providing the test engineers with remote visualizations of the sensor readings, while protecting them from the large rotating equipment.
A comfortable customer viewing area is also available, from where they can watch and interact with the test engineers before hand over to ensure that the machine meets the required performance levels. The entire process is transparent and straightforward.
Static tests can be run to check winding resistance, insulation resistance and surge comparison test to test the stator of the machine.
When checking a machine under full load, a much more comprehensive picture of the motors required performance can be built up. The test is particularly relevant to check critical machines that are going to be difficult to return to the workshop after fitment either due to location, confined space, lifting gear requirements, shipping, offshore etc. Tests can include efficiency, noise and temperature rise measurements, indirect load tests, excess current, torque tests, and torque/speed tests.
Sulzer has invested in a controlled environment. On site testing where the environment cannot be controlled, will throw up a lot of uncertainties in the readings, leading to unreliable results. Getting a machine up to normal running temperature can take 4 to 6 hours, and to keep a machine on full load on site could be difficult.
In a controlled environment, the ambient temperature is known, while the load can be accurately applied. There is also the benefit of being able to test the equipment for a full working day or over an extended period.
More importantly – the test bed’s stiffness is known and factored against the machines vibration and noise levels, whereas on site vibrations would cloud the results. Another aspect to consider is being able to measure the temperature of the windings within 2 minutes of stopping, which is much, much, easier to do in a controlled environment, resistance temperature detectors don’t always give the complete story.
As part of the upgrade project, the test area was equipped with the latest monitoring controls and safety equipment, providing the test engineers with remote visualizations of the sensor readings, while protecting them from the large rotating equipment.
A comfortable customer viewing area is also available, from where they can watch and interact with the test engineers before hand over to ensure that the machine meets the required performance levels. The entire process is transparent and straightforward.
Facing the Challenge
Despite the understandable challenges of keeping the facility running without disruption while major works took place; there were many options to decide upon when designing the new system to satisfy customer needs and be a showcase for Sulzer.
Falkirk is used to seeing a mix of offshore motors from the oil and gas industry, which usually operate at a 60Hz frequency, whereas onshore equipment runs at 50Hz meaning a dual or variable frequency system was required.
A wide variety of voltages from 400V to 13800kV had to be catered for, as well a variety of speeds from 2 pole to 8 pole. The testing of back to back, multiple motors, vertical motors, old machinery, and induction motors, were all further challenges to overcome.
When it came to engineering the test bed’s capabilities of handling induction motors, frequency variations needed to be accounted for. A standard grid power supply of 50Hz fed through a transformer provides a variety of voltages to the induction motor. Due to slip, the motor runs at a slightly lower frequency meaning the power from the generator running at 1485rpm gives only 49Hz, which of course, can’t be put back into the grid.
There were two solutions considered to handle induction motors. A variable speed drive (VSD) could be used to bring the frequency back up to 50Hz for the grid. VSDs can cause spikes in voltages that modern motors are designed to handle, yet older equipment would not. VSDs also create additional harmonic, noise, heating and vibrations which will affect test results.
A more reliable option was to choose a fixed frequency diesel generator set fed into the test facility from outside, offering a constant sine wave without any voltage spikes. The controlled conditions mean momentary overloads can be handled and starting currents can be monitored for asynchronous machines.
Doubling capacity
Until now, the Falkirk site used a 1,250 kVA diesel generator operated through two step-up transformers to provide 3.3 to 11 kV via high voltage switchgear to the test bed. The new investment adds a 2,000 kVA and a 700 kVA generator to the site, synchronized through a 4,000 Amp low voltage switchboard, as well as a new 2,500 kVA transformer, doubling the capacity of the test bed.Of the original 1,000 kW capacity in load testing, 800 kW can be used for testing vertically-orientated machines, across the full range of voltages from 400 V up to 11 kV at both 50 and 60 Hz. The new installation increases the load testing capacity to 2,000 kW for horizontally-orientated motors as well an increase in voltage to 13.8 kV. Most of the equipment tested in the increased capacity will be large, high voltage, AC motors, but the possibility to test DC motors up to 600 V, with a loading up to 800 amps remains.
With the expanded test-bed in place, multiple motors can be tested alongside each other. Meaning if the testing of one motor needs to be extended, other projects won’t be held back.
The new test bed also offers the possibility of load testing generators using a slave motor to turn the generator and connecting the output to a load bank. In this way, generators having undergone major repairs, and can be tested to ensure that they are fit for purpose before they are re-installed and recommissioned.